Or, the bottom of the rock foundation, to be more precise.
And the low point of the build, insofar as the mass of the house recently got as low as it is expected to be during this project.
Which means we are moving into the “adding back” to the original ~30’X40’ house that Moses Chaplin built, including the second floor that the Forbush family added in the 1800s. It is an exciting inflection point!
The fall colors provide a spectacular backdrop to the work. The trees, seemingly ablaze in the fall sunlight, are striking enough that just about every day someone on the job site comments on them.
The brilliant leaves, and temperatures regularly dipping into the 30s at night, also serve as a reminder that snow (and hard freezes) is not far off. These signposts of seasonal transition keep the primary goal for the fall building season–getting the existing structure “snugged up” for winter–in sharp focus.
We’re currently a ways away from “snug”, with the building now essentially being a timber frame structure with plaster walls on the inside, with four inches of uninsulated space covered only by board sheathing on the outside. The dining room wall was a notable exception to the structural state I just summarized, as it recently passed through a phase with no wall whatsoever—the Snowdog team has since remedied the situation admirably—we now have a framed wall where that hole is below!
There remains a roof (mostly–and that is coming off), electricity, and running water. And heat from the fireplace insert. Flannel, down comforters and hats work just fine for now.
But with no alternative heating source, less insulation than we had last winter…and shortening days, the race is on!
Getting the building “snugged” up for winter means the following:
Finish repair of all the spots with rotten wood–most notably, the sill beams and the aforementioned dining room wall. Most of this is now done. If you look carefully at the picture above, you can see that the dowel/wood hardener approach discussed here worked really well to repair many of the partially rotted sill beams.
In some spots, the sill beams were rotten through, and required replacement in sections. Skye made a copper plate to commemorate the Snowdog team’s work to join “the old and the new”. We mused about some future folks coming across this and wondering what life was like way back in 2022, and who these Snowdog people were that left their mark on this house! “Fat out” the walls (outward), and roof (upward), and then insulate the newly created space. We are basically putting a jacket and hat on the house. At risk of torturing the metaphor, next year we will put on leggings/socks when we insulate the basement.
Frame up the porch that is to be added to the front of the house, so that the roof on the house and porch can be tied together seamlessly.
Replace the existing windows with triple glazed, air tight windows to be set into the fattened out walls.
Cover the walls and roof decking with a water resistant barrier, so that it can take the snow and rain until the exterior cladding is added next year.
Work out a temporary heating system to get us through this winter (next year we will trade out any fossil fuel solutions for heat pumps and a wood stove backup)
Completing 1-6 will allow us to live in the house this winter. Plus, the work of Bill, Jason and their team on excavation/site prep, and Lucas and his team at Gendron Construction on getting the concrete1 foundation poured for the addition prior to winter, will leave us in a strong position to have a flying start in the spring.
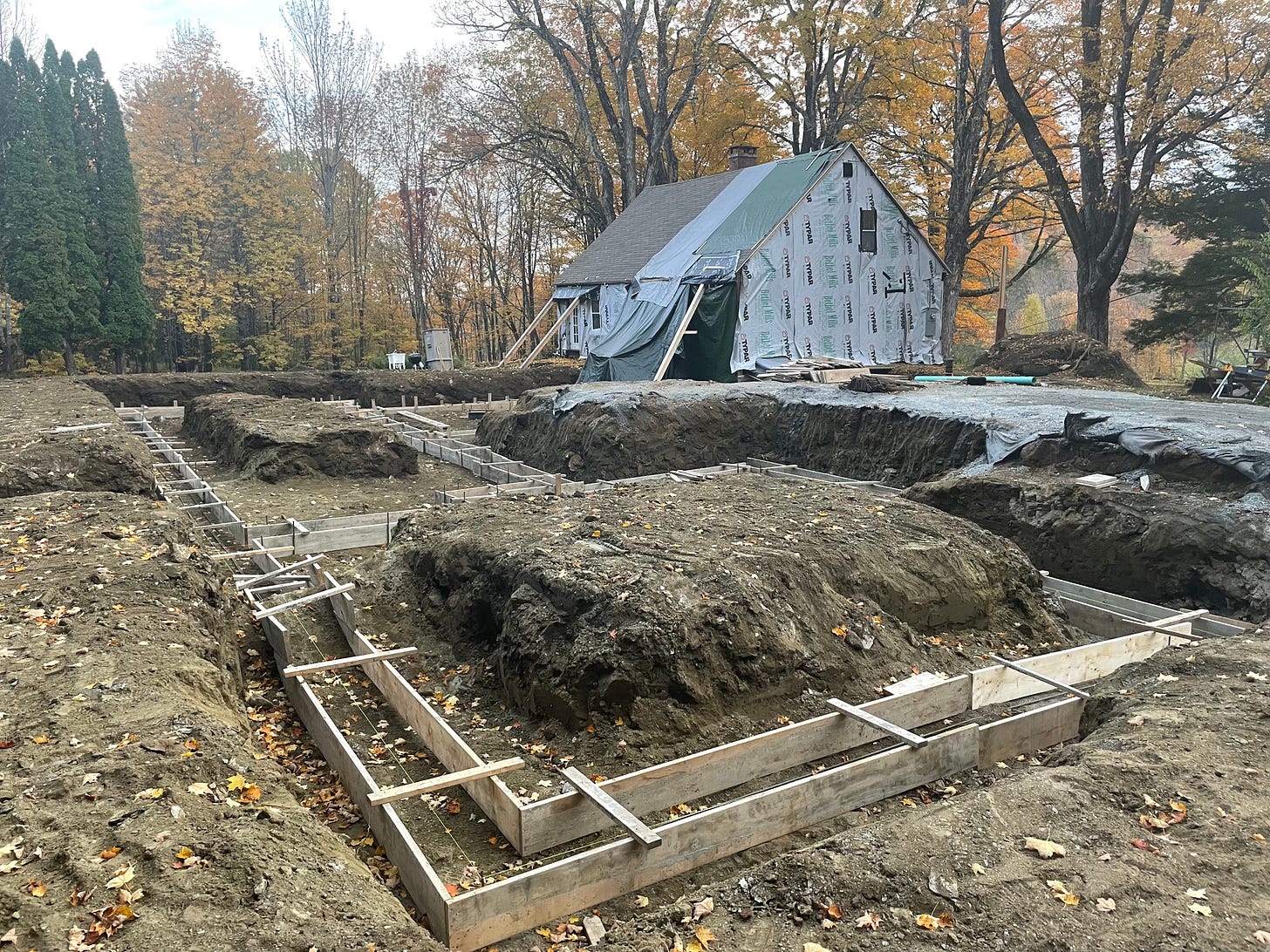
About “rock bottom”....
The plan to fatten and raise the pitch of the roof calls for a new ridge beam set up above the existing roof ridge, and supported by posts that run down to the ground; two of which will snug up against the existing house on the gable ends. In order to have them be stable, those posts need to rest on a concrete pier that extends below the frost line. Easy enough–excavate two fairly small (2’ X 3’) holes so that the pier can be formed up against the existing foundation and tied into it, and we’re all set!
“All set”, except for the fact that the original foundation of this house is fieldstones stacked on top of each other with no mortar, which means three things relevant to pouring a pier that hugs the foundation (and is structurally connected to it somehow):
the stones are irregularly shaped, and many stick out away from the house, so you can’t dig a hole close to the house for the pier without removing many stones
most of those stones are too small to find a way to easily connect the new concrete pier to the stones, which quickly became moot when we saw that….
when you remove one rock, because there is no mortar, other rocks start tumbling out, resulting in a hole in the foundation that grows exponentially with each stone you remove.
That last point is an exaggeration–it wasn’t exponential. But I assure you that when you are standing in a 6 foot deep hole, with the foundation falling down around you, neither the mathematics of hole size expansion, nor the physics that says the building really won’t collapse as that amount of foundation is removed, is of any comfort!
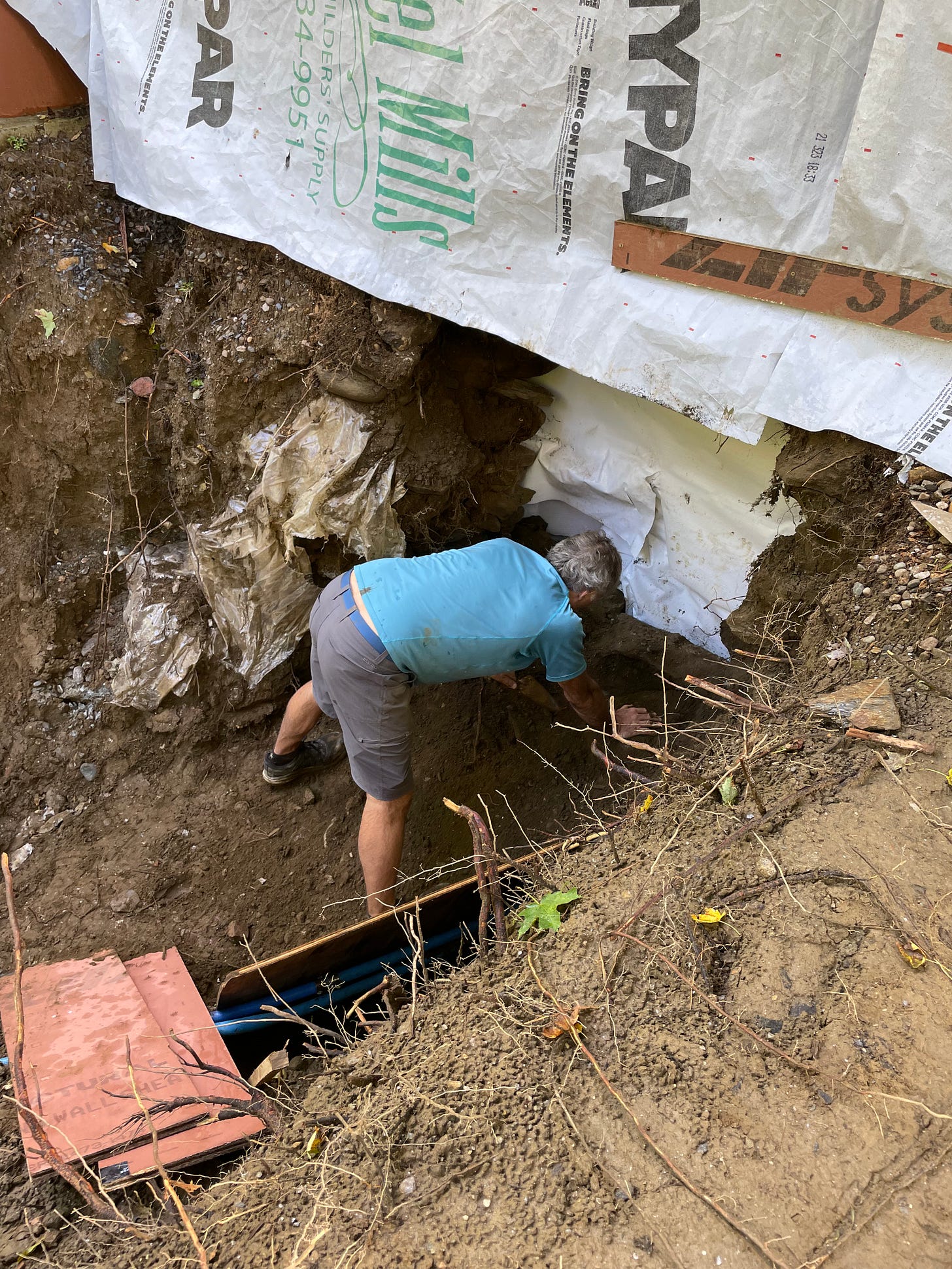
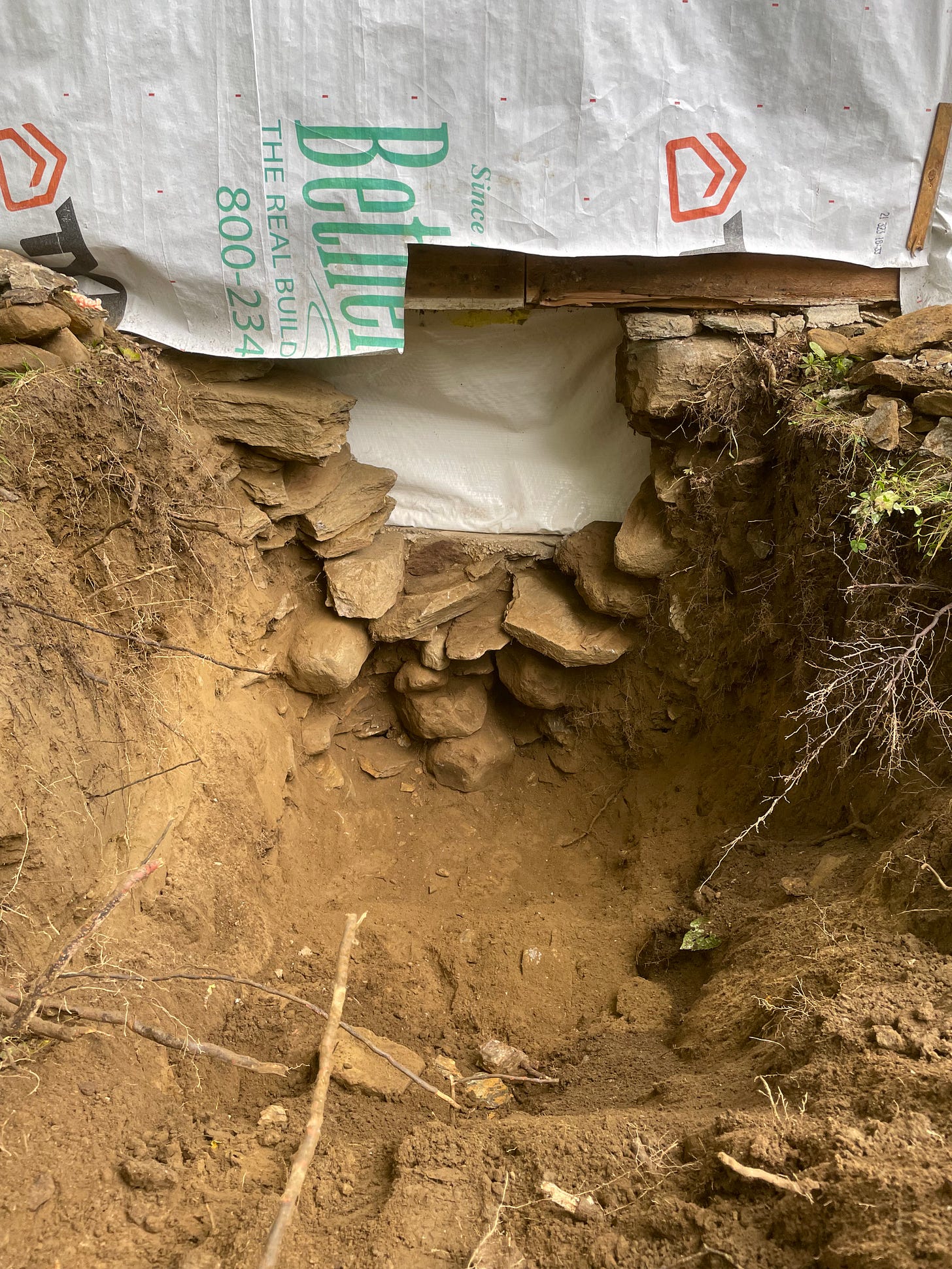
We got it done by digging down to the bottom of the foundation (and then some), removing the stone, and then the concrete team formed and poured a pier, as well as a new section of foundation wall, that provides nice landing spots for the posts that will support the roof.
Now, we are truly ready to start adding back to the building—let construction begin!
Concrete is one of the biggest sources of carbon pollution that is used in building materials, and so contributes disproportionately to the “embodied carbon” of a new building (as discussed previously). As such, we have taken a number of steps to minimize the carbon impact of concrete in this project by: (1) reducing concrete use in the build by (a) eliminating the concrete slab in all sections of the new build except the garage, and (b) reducing foundation wall thickness from the typical 8 inches to 6 inches (2) using concrete that contains 50% slag in the mix. Slag is a waste product from refining metals, which can be added to a concrete mix to reduce the amount of Portland cement required to get a strong finished product. As Portland cement is by far the biggest contributor to the carbon pollution profile of concrete, making this switch reduces the carbon impact of the concrete by nearly 50% as well. There is no increased cost in making this choice—and I appreciate Lucas working with Carroll concrete to ensure we could get 50% slag concrete for the build. I will do a full accounting of the embodied carbon in this build at a later date, but suffice it to say that concrete is the biggest drivers in the “minus” column. And use of dense packed cellulose for insulation is similarly one of the biggest drivers in the “plus” column for this build, by stashing plant-derived fixed carbon for what we hope are many, many years.