9,725 pounds of weight gain in three days. Looking from the outside, you simply can’t tell. But from the inside….oh my!
I’ve written elsewhere about the concept of putting a jacket and hat on the original house that Moses Chaplin built. In brief, it involves building a straight level and plumb frame around the decidedly NOT straight, level and plumb original house. Then, the new exterior frame is covered with plywood sheathing, resulting in empty cavities between the old (now interior) sheathing and the new exterior sheathing. These cavities are then insulated—a newly insulated roof is the “hat”, and the insulated walls are the “jacket”.
The work thus far was exacting, including many custom measurements and cuts, dealing with the southward lean, sill rot, and the rest. And at the final step of sheathing the new frame, the Snowdog team was especially attentive to air sealing to ensure a continuous, intact air barrier (air infiltration is a major cause of discomfort, heat loss, moisture issues, and the like). It is important to get air sealing right–so much so, books have been written on the subject, including “A house needs to breathe…or does it?”
The effort yielded a new frame and “skin” on the outside, and empty cavities in between the new and old walls and roof.
The final step to put on the hat and jacket was to stuff the cavities with insulation!
Our insulation material of choice is cellulose. Why?
Amongst other reasons, cellulose:
Traps carbon pollution. Plants use atmospheric carbon dioxide (a greenhouse gas) to make sugars via photosynthesis. One of those sugars, glucose, is strung together end to end by plants into long chains to yield cellulose1. Cellulose is used to make paper and related products (e.g.-cardboard). Recycled paper and cardboard, when chopped up into small bits and put in the right places in a building, is a great insulation.
To recap…atmospheric carbon dioxide is pulled out of the air by plants, and ultimately makes it into the walls and roof of the house as cellulose insulation. So, for as long as the house stands (centuries, we hope) that carbon remains locked in the house, and can’t be a greenhouse gas.
Many other types of insulation in common use today can not claim this carbon trapping property, though there are a few–and some exciting newer ones gaining traction. Like straw bales. And wood fiber insulation (our partner Bensonwood will be using this wood fiber insulation for the new part of the house, in addition to dense packed cellulose)2.
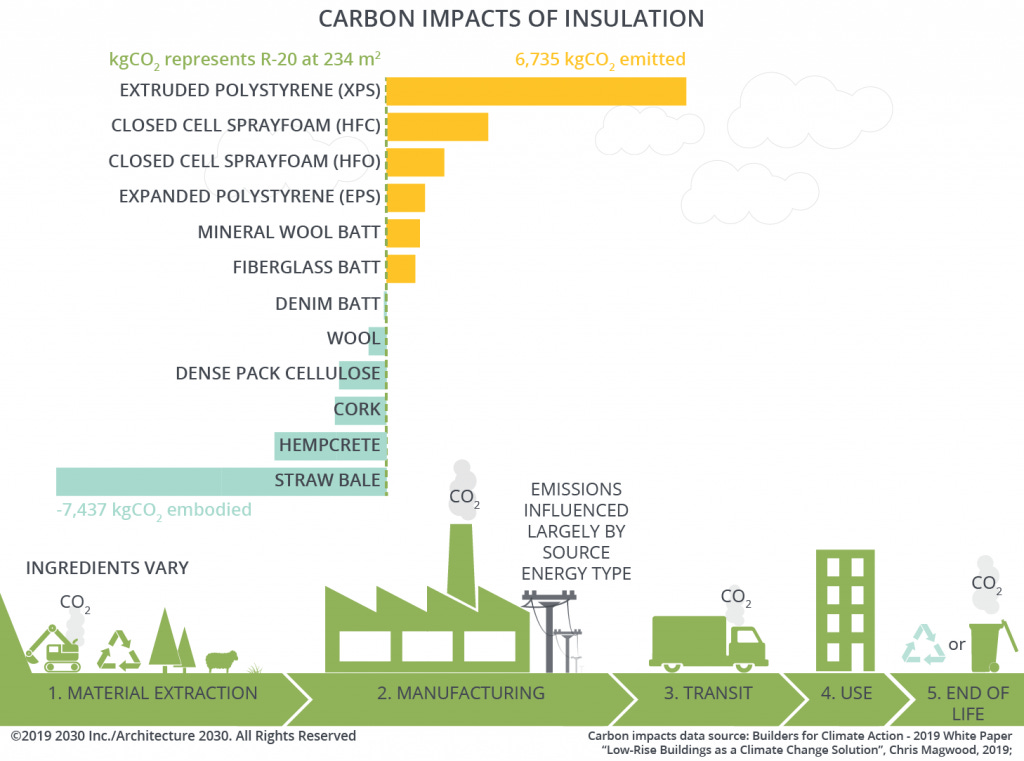
Manages moisture. Cellulose reversibly adsorbs water vapor under humid conditions, and releases water vapor when humidity decreases. Managing water vapor in a home to prevent inappropriate condensation and subsequent mold growth and rot –especially in “tight” homes that are well airsealed and insulated–is a major issue. Cellulose helps do so by serving as a “vapor buffer” within wall and roof assemblies.
Does not contain toxic volatile chemicals that off-gas for days, weeks, or longer. Spray foam…not so much. There is a reason spray foam installers ask homeowners to remove themselves and their pets for 24 hours after spray foam installation. he green building community has PLENTY of reasons to want to avoid foam in most all applications. You could start with this relatively recent article from VT Digger if you want to know more.
Helps block fire spread. This is counterintuitive (paper burns after all!), but the borate added to cellulose insulation acts as a fire retardant, in addition to inhibiting mold growth and repelling rodents and insects. Check out this dramatic demo to see just how well cellulose insulation resists ignition and dramatically slows heat transfer.
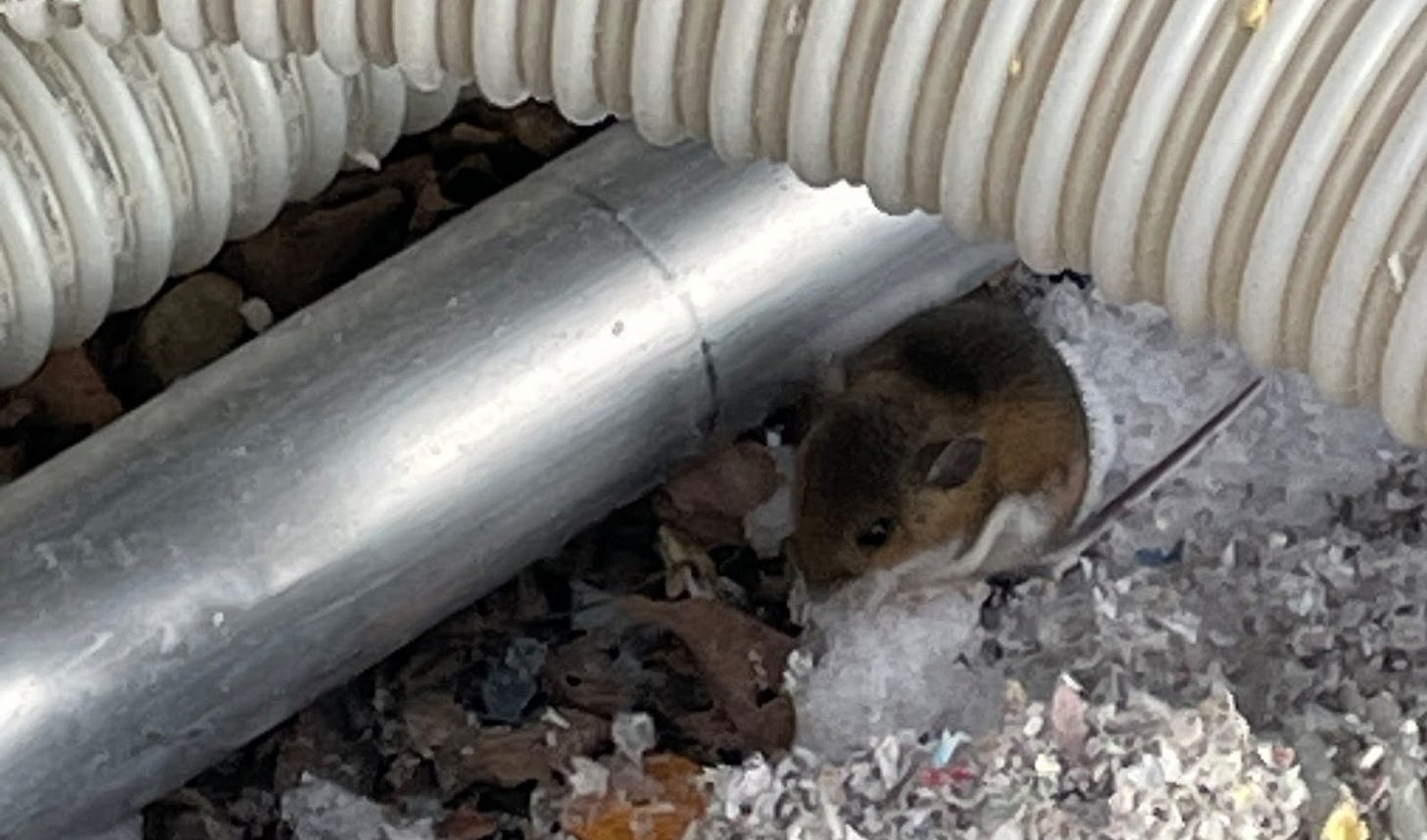
Attenuates sound. I love my neighbors. I’ve come to recognize the sound of each of their cars, and notice the rhythm of their daily routines when they drive by the house. We don’t get much in the way of traffic, at least outside of leaf peeping season, so one tends to notice. But the morning after we insulated the wall facing the road, all was quiet. No 6 AM truck heading off for a busy work day. No 8:45 AM run to town. No post office van speeding by late in the afternoon. I first thought I had just been distracted, but then realized just how much quieter the house was. Guess I will have to set my alarm for 6 AM from now on!
Comparatively inexpensive. Self explanatory.
Yay cellulose3!
The process
To get the cellulose where it needs to be, cellulose bales go into a machine with two big augurs that break up the bales into a “fluff” which is then blown through long hoses into the wall and roof cavities. For loose fill/semi-dense applications (like the roof), this can go very quickly. Indeed, with Skye and Dylan up on the roof with the hoses, Nell and I were filling the hoppers on the two machines at a quick pace! When dense packing (to create a self supporting vertical stack of cellulose, like in walls, so that it doesn’t settle over time) smaller hoses are used at the business end, and the mix is adjusted to provide more air/less material. The process slow downs a lot at the machine end when dense packing. This leaves time for the people filling the hoppers to do things like write blog posts.
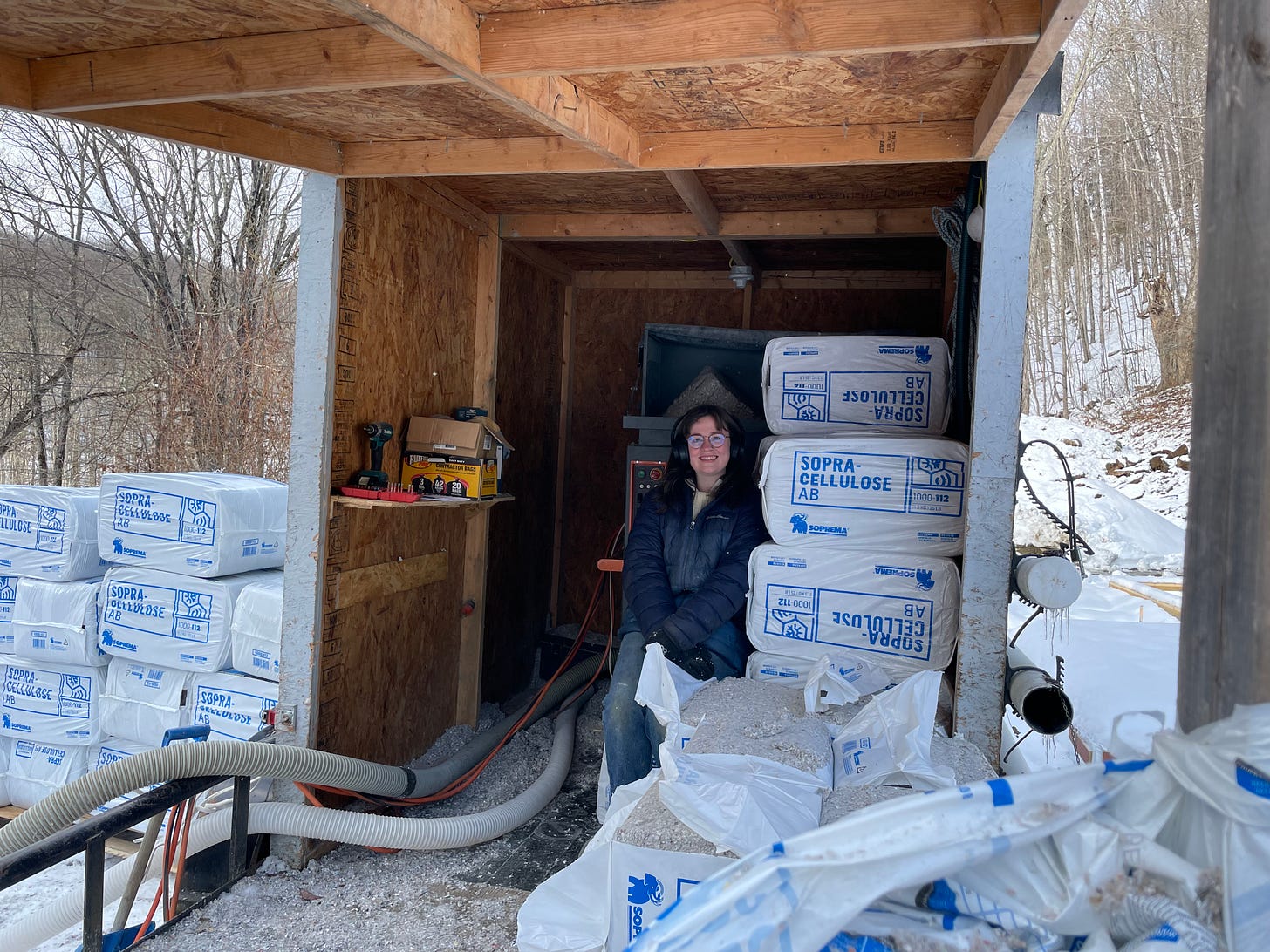
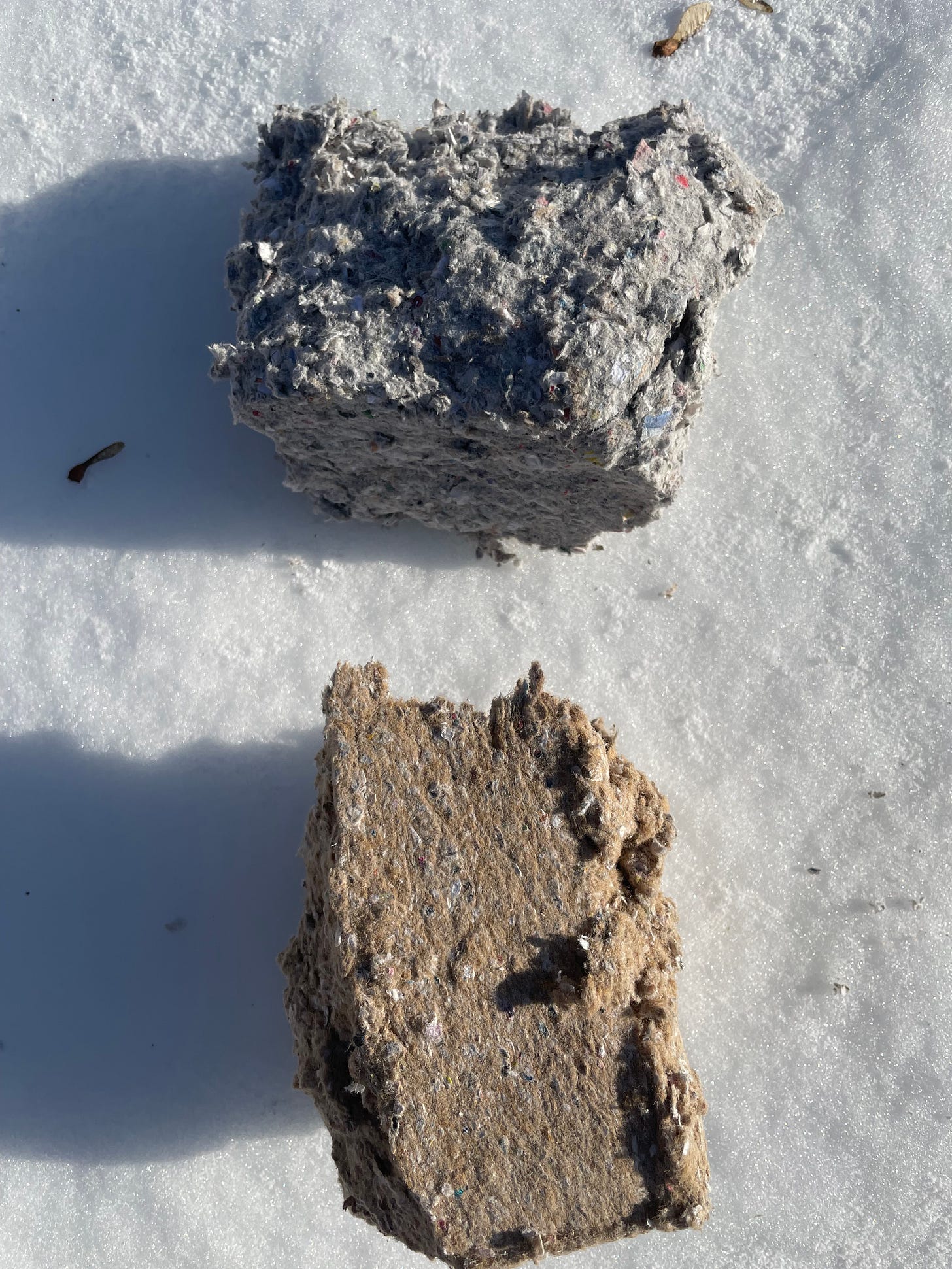
The jacket
The jacket (wall insulation) is at least 12 inches of cellulose. “At least” because the southward lean of the original house around which we built a straight level and plumb structure means that the top of the north gable end and the bottom of the south gable end are significantly further than 12 inches from the new outside wall. Plus, Ed added 14 inches minimum on the north gable end (versus 12 to the south) for architectural reasons. This all means that the insulation jacket ranges in thickness from 12 inches at a minimum (south wall, bottom) to as much 25 inches (north end, top) on the gable ends. The eave ends (east and west) are considerably less variable, and accommodate pretty close to 12 inches of insulation everywhere. For those who like to talk about insulation in R-values (a measure of resistance to heat transfer), the eave end walls are roughly R-44 throughout, whereas the gable end walls range from at least R-44 to as much as R-91. Wall insulation target levels by Vermont code is R-20.
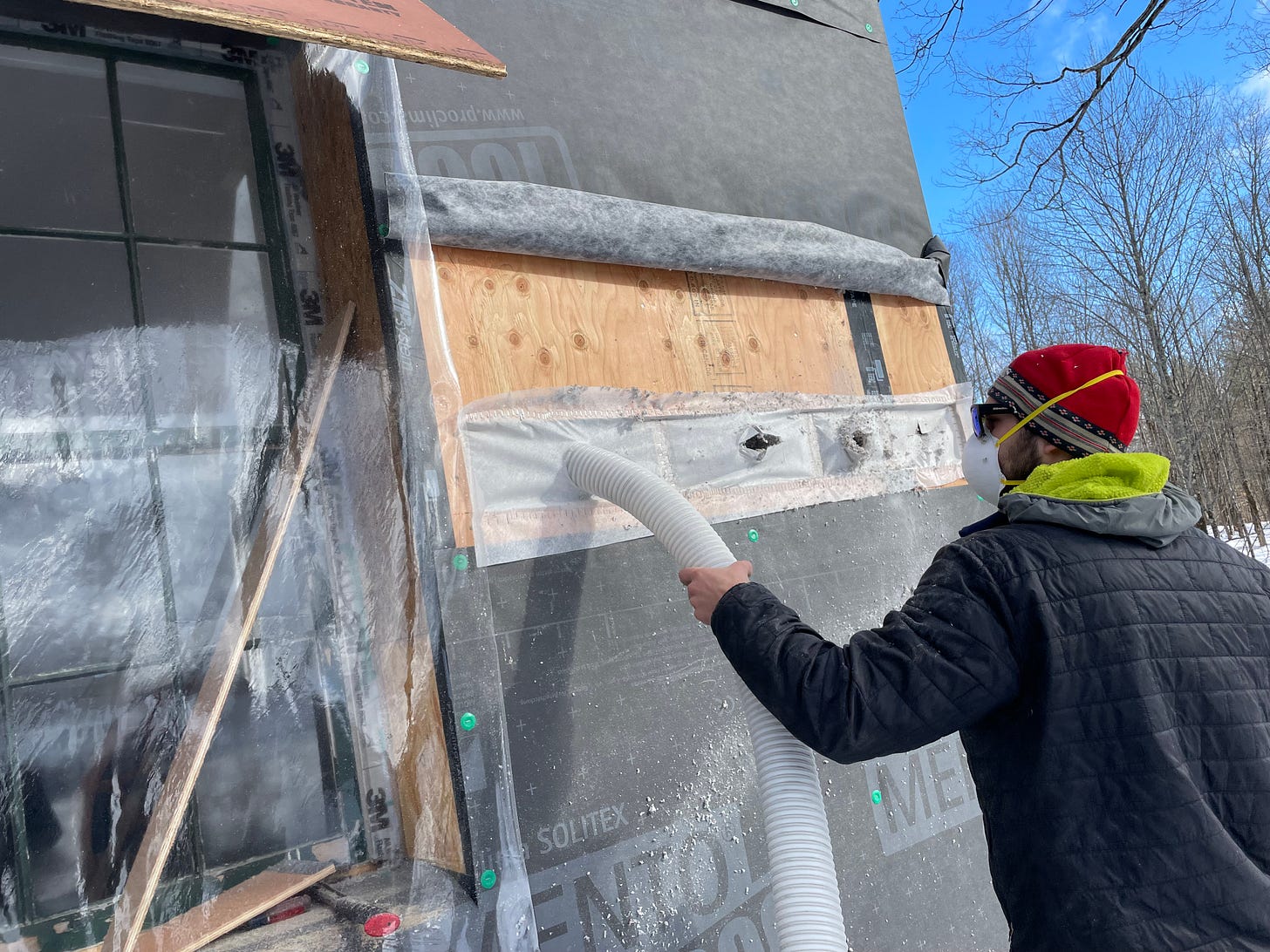
The hat
Given the propensity of heat to rise, the hat (roof insulation) warrants a greater thickness than the walls. In our case, insulation depth is about 20 inches at the eaves and 30 inches at the peak. This variation is because we chose to build a steeper roof over the top of the original roof, so the distance between the original roof and the new roof deck grows from eave to ridge. The corresponding R-value is about R-62 at the eaves and R-93 at the ridge. Sloped roof insulation target levels by Vermont code is R-49.
The sudden weight gain
As of this writing (about two days from completion of insulation), the original house had received 7,125 pounds of cellulose insulation in the roof, and 2,600 pounds in the two completed walls (west and south). When I first reflected on the roof number, it occurred to me that we’d just added a weight equivalent to two RAV4s (the car I drive). Two of my cars plopped (okay, melted down and evenly distributed) onto a 240+ year old timber frame.
The structural engineer, who knows much more than me about such matters, was perfectly happy with this plan, as were Ed and Michael. And I trust them! Of course I do.
But just to take the edge off, I did a little internet sleuthing.
Turns out, 7,125 pounds is roughly the equivalent of about 12 inches of damp snow on this roof. That was quite reassuring, as we’ve seen twice as much on this roof on any given winter, and I am sure the Chaplins, Forbushes, Eastmans and Copelands, George and Mary and their descendants saw plenty more in their time!
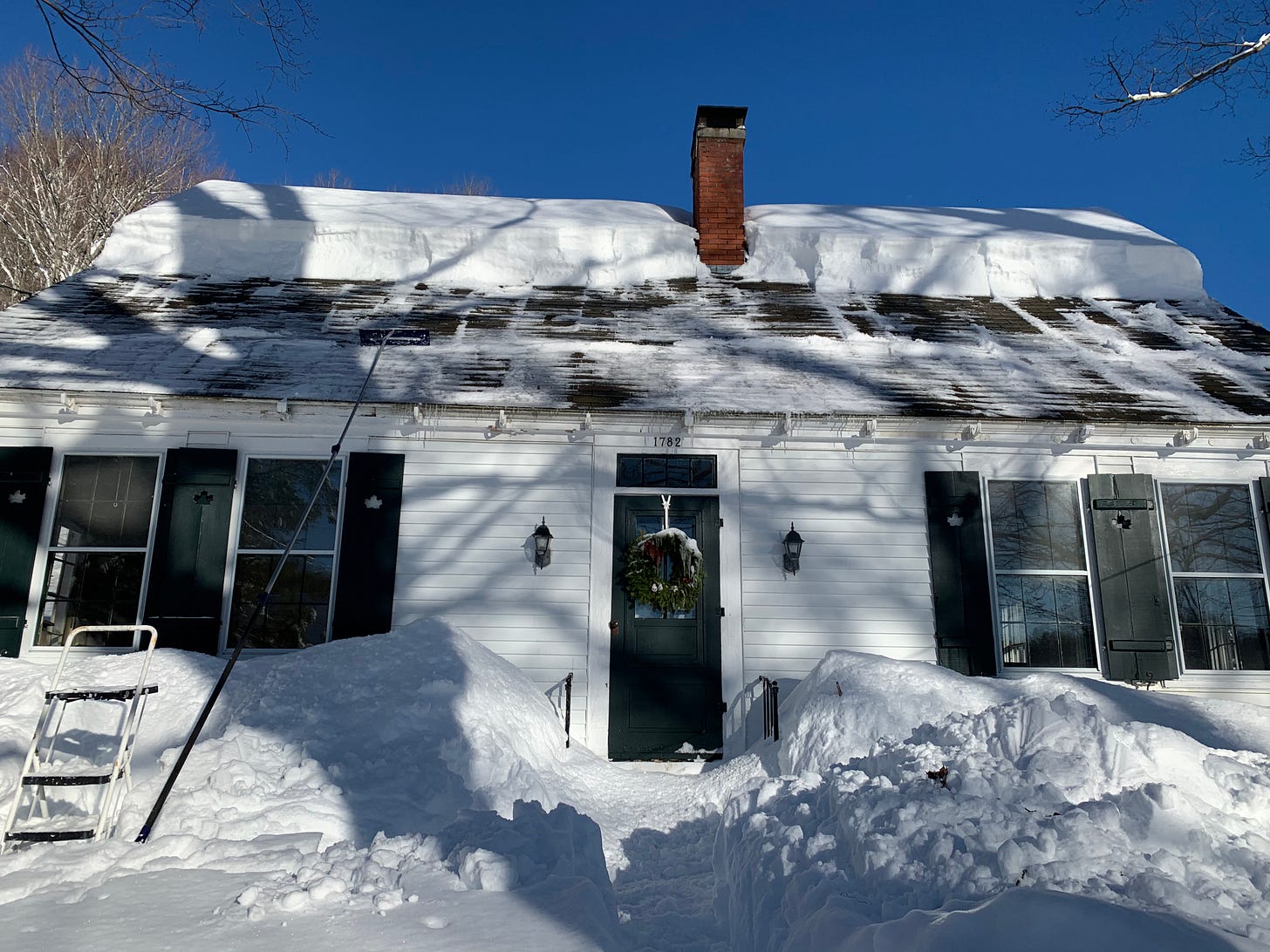
But you know what was even better than that feeling of relief?
The feeling inside the house.
Before we insulated, there were nights when our bedroom—which is now the living room since we’re renovating the upstairs–would get into the low-40s at night. Not quite in equilibrium with the outside, but close. Of course, the room really only had three walls (the fourth being two sheets of plastic), and we didn’t have heat directly in that room since we removed the fireplace chimney. Let’s just say it was brisk, and getting out from under the covers required a deep breath before jumping up to greet the day!
We still have a partial, uninsulated wall in the bedroom/living room as of this writing. However, with two of the three exterior walls insulated, and the roof fully insulated (except for the dormers), interior comfort is transformed.
Where previously outside temperatures in the low 20s would drive the bedroom down to the low 40s, it is now easily holding 60 degrees when the thermostat (located in the dining room, on the other side of the house, and closest to the heat source) is set to 57. And the upstairs bathroom, in which I sometimes wondered whether I would find a frozen toilet bowl to greet me after a cold night, has matched the thermostat setting quite nicely. And that is without a direct heat source upstairs.
I even caught myself walking around in a t-shirt on a recent 13 degree morning, and passive solar heat gains from the south and west windows in the living room/bedroom mean that we can get into the mid-60s with that same 57 degree thermostat setting.
I’m sure my southern relatives will be shivering just thinking about these temperatures…but we find it extremely cozy already.
All this relative warmth in a house without a structurally complete exterior wall on one side, insulation in the dormers, or higher performing windows and door. So, we’ve plenty of fossil fuel free thermal comfort and efficiency upside to come!
A few other morsels
We’ve completed framing the floor system for the addition, and have “put that to bed” until Bensonwood will arrive to assemble the addition on top of that floor system–very soon!
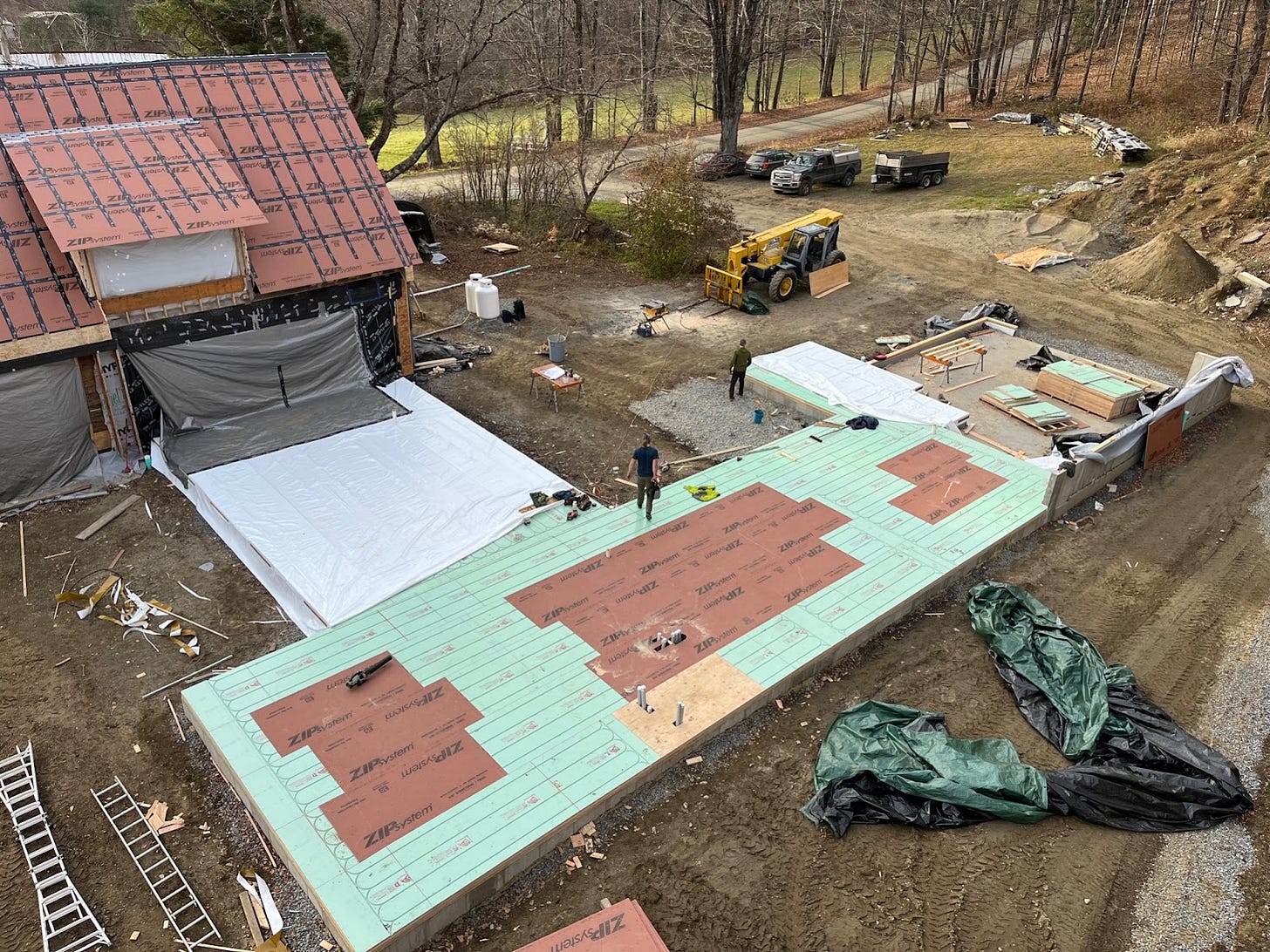
The Bensonwood team has begun assembling the elements of the addition as of this writing. We are looking forward to our visit to Bensonwood to see our walls and roof panels being built!
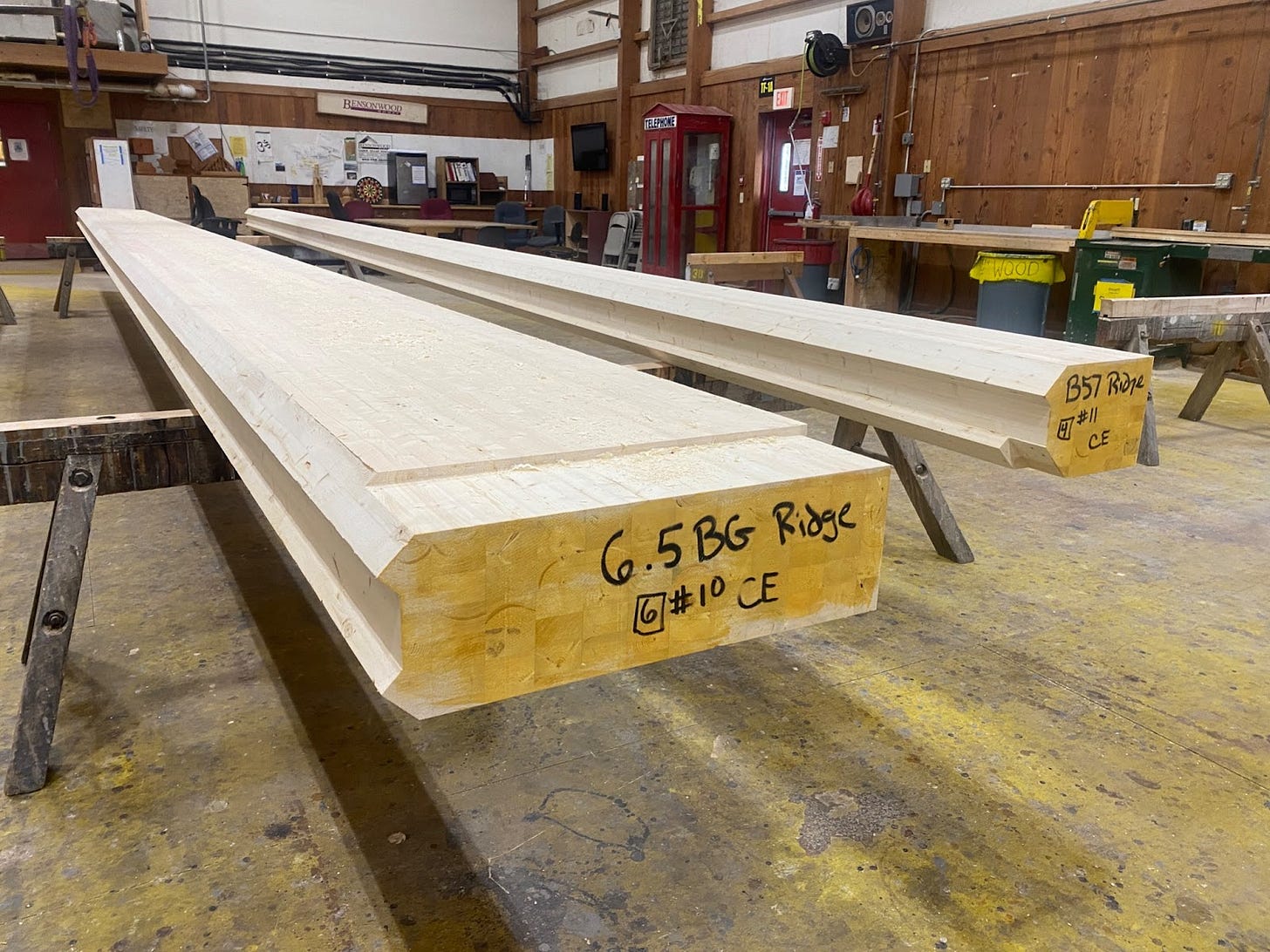
What distracted me from finishing the blog today.
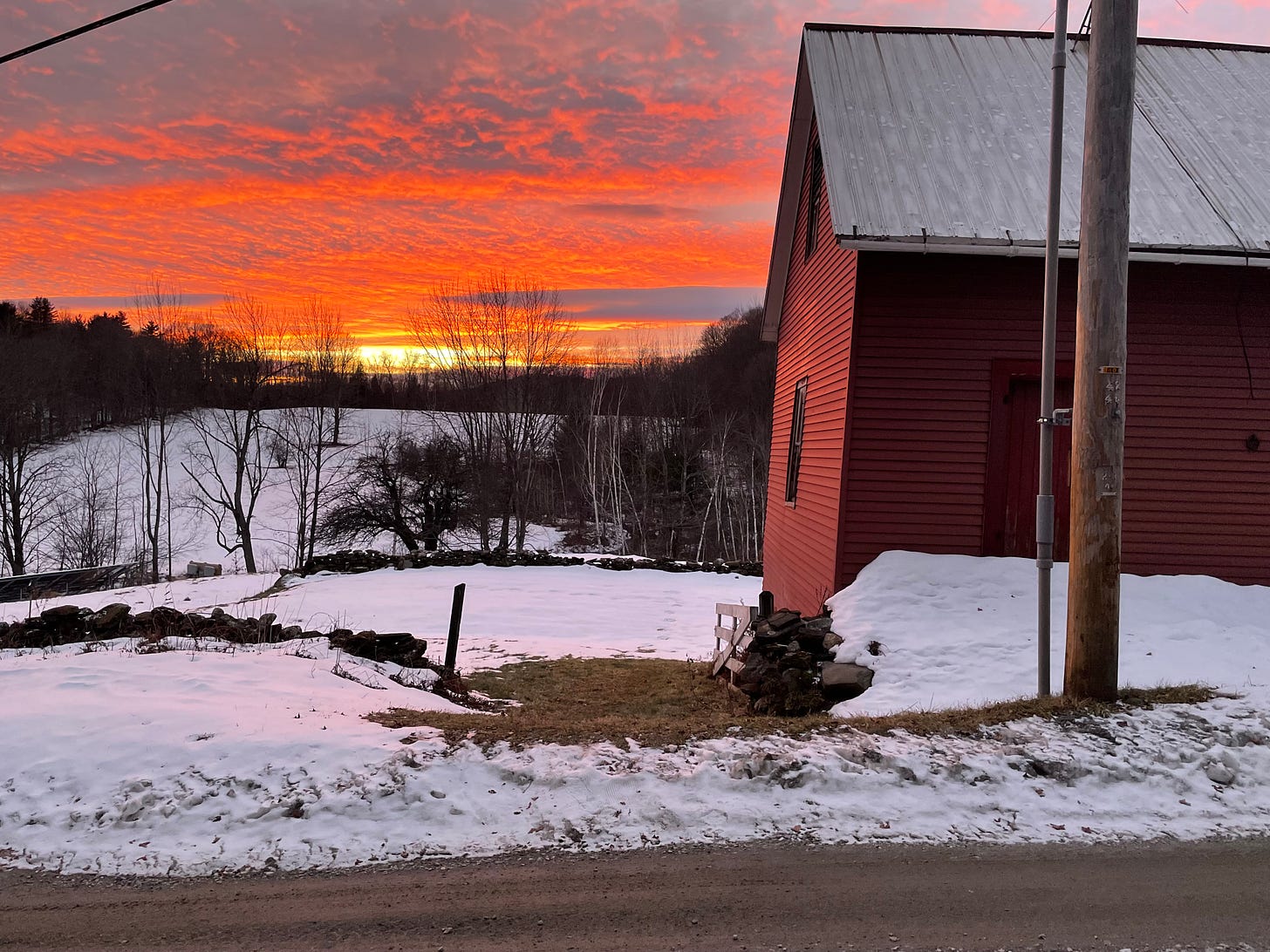
In cellulose, every glucose molecule in the chain is rotated 180 degrees relative to the ones adjacent to it. If the glucose molecules in the chain are instead all oriented in the same way when linked end to end, a molecule with very different properties results. Starch. Digestible by humans, useful in its own ways…but not a good insulating material!
For more on building materials that help trap carbon versus emit, check out this 2021 report. This is a rapidly evolving area, so it pays to stay abreast of what is happening when considering a new project.
Michael, and his colleague and friend Bill Hulstrunk (a cellulose expert, amongst many other things building science–and also advisor/friend to this project), have given many talks on the benefits of cellulose. Here are the very informative slides from one. It addresses the points above and much more. I’m on the cellulose bandwagon now too!
Well that is a lot of weight for one to gain in a week, but it will keep you warm and cozy. Very interesting that paper and cardboard can be used as
Will this type of insulation condense down in the roof area after a few years that you will need to reinstall new insulation?
Another great read on the reconstruction of the house, and the inner workings of what is behind the walls.
Brian, this is a real gem. An amazing amount of important information. The teacher in you coms through crystal clear. It looks to me like you’re doing a wonderful job of drafting chapters to a book. I’m so impressed and delighted by your work.