Job site conditions for building on December 21st in this beautiful part of Upper New England were perfect: 68 degrees, 50 percent relative humidity, no snow/rain/sleet/wind to worry about, good light from 7 AM to 5 PM. The Snowdog Construction team was ready to go!
“Ready to go”....watch, that is.
On the shortest day of the year, the Snowdog team and collaborators took a field trip to observe our partners, Bensonwood, work their magic inside their 110,000 sf fabrication facility in Keene, NH. As described more fully in a separate post, we had partnered with Bensonwood to build the addition to the original house that Moses Chaplin built. Bensonwood’s offsite panelized construction process offered the opportunity to quickly and efficiently create a high performance building shell that matched our intended design.
When we arrived at the Bensonwood facility, it was 20 degrees outside, with snow on the ground, and rain and snow forecasted for the coming weeks.
But inside, it was balmy.
A great day for building, and a great day for a tour.
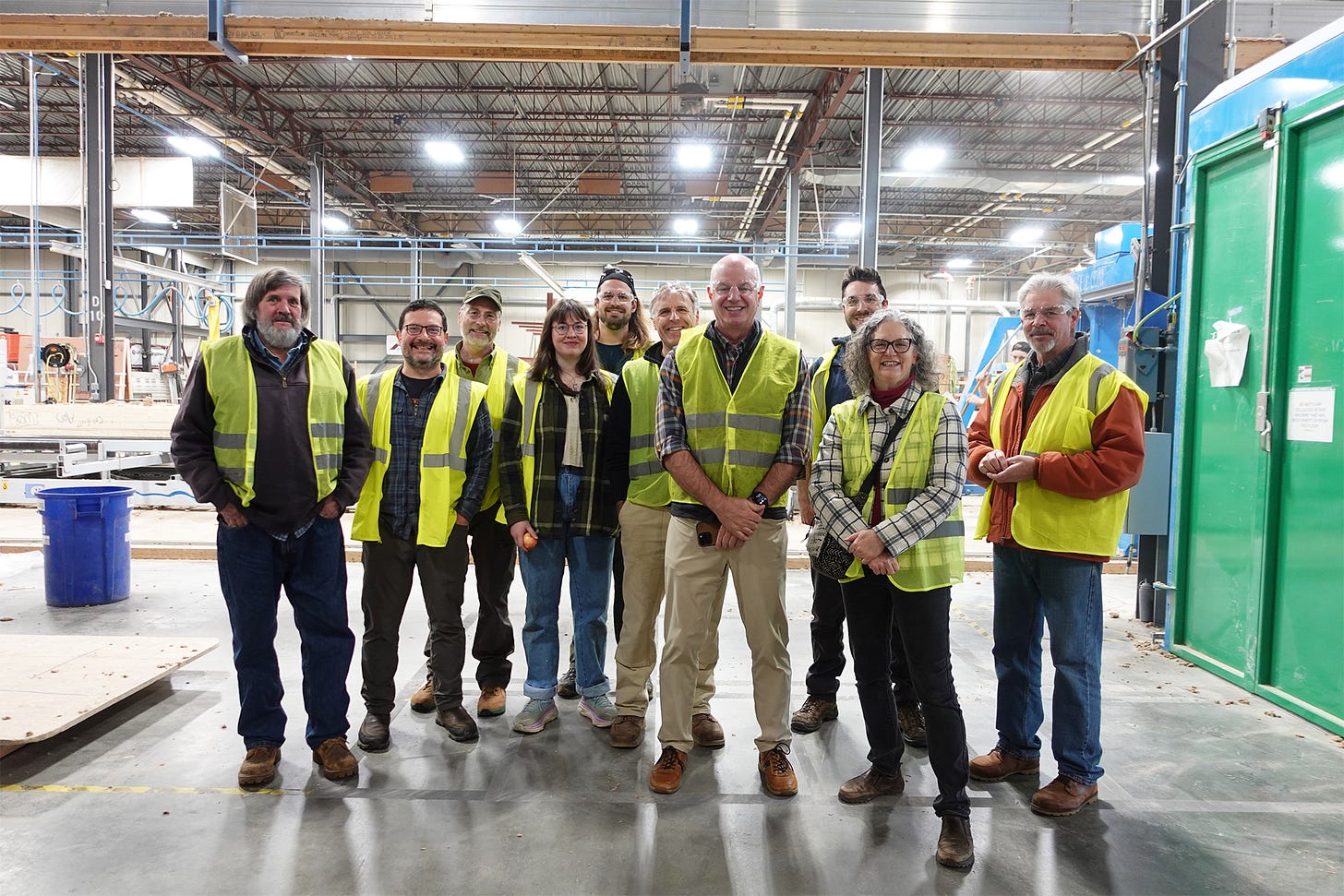
Welcome to “wall and roof panel” and “window install” day!
First stop was the material staging area, which is large enough to store all the materials for our project, and MUCH more. Being able to store materials inside, so they don’t get wet, swell, warp, etc., really helps with Bensonwood’s precision building process. When you are counting on lining up fully insulated (multi-thousand pound) panels out at the installation site to create an integral wall and roof assembly–in all kinds of weather conditions–it sure helps to have materials that have been built exactly as the plans specify!
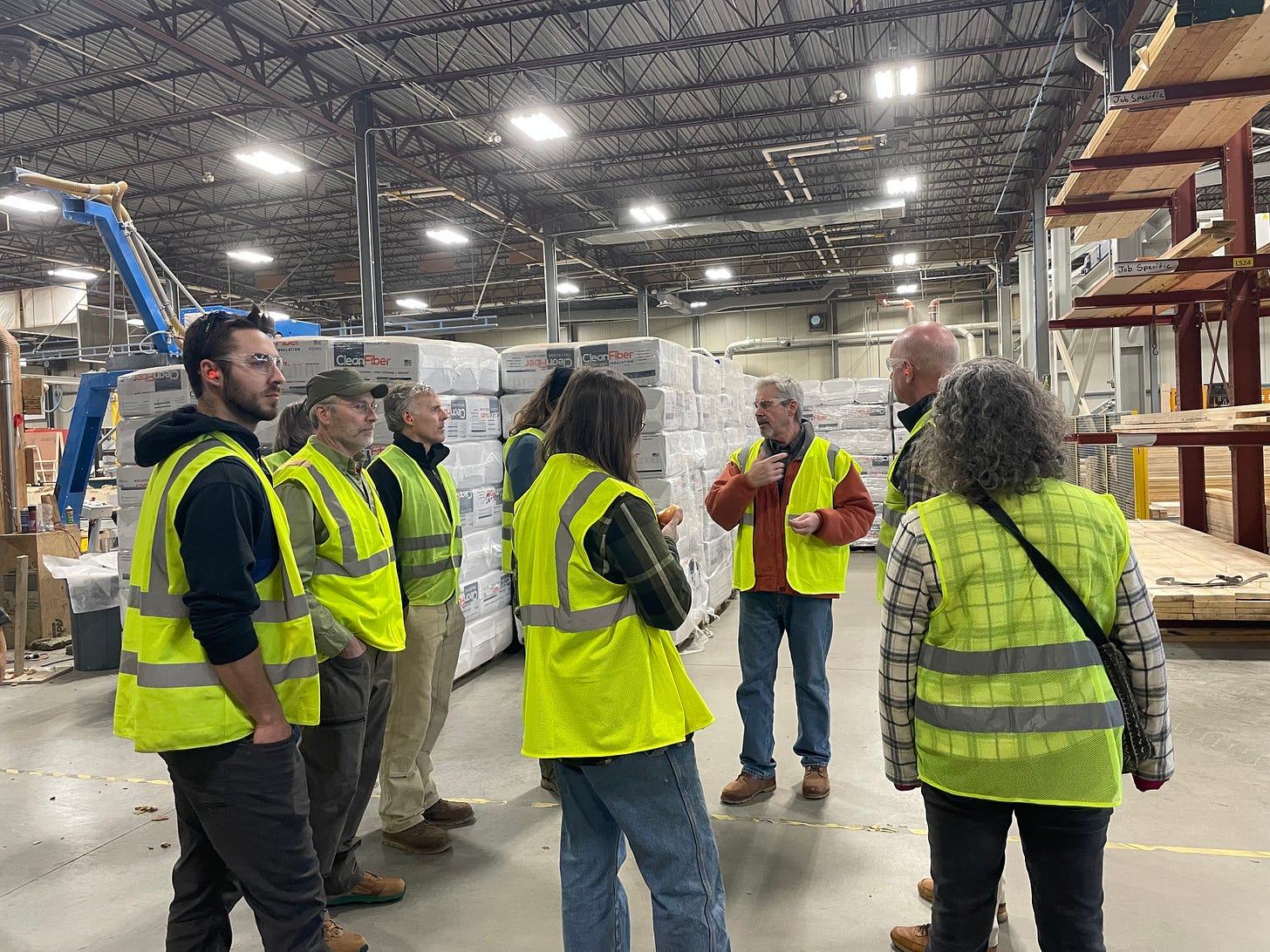
Next stop, the Hundegger Speed Cut SC-3: where “virtual fabrication” drops the “virtual”
At the outset of our collaboration, Bensonwood coordinated closely with our architect Ed to translate his concept into their system (special shout out here to Aaron and Florian at Bensonwood for their work here). After finalizing the design, the project moved into a “virtual fabrication” process, during which Bensonwood created an exceptionally detailed digital 3-D model of every aspect of the build. Precise dimensions for every piece of lumber. Every angle of every cut. Every nail and screw and hanger. Every penetration for plumbing vents, exterior outlets, ventilation. Every…everything.
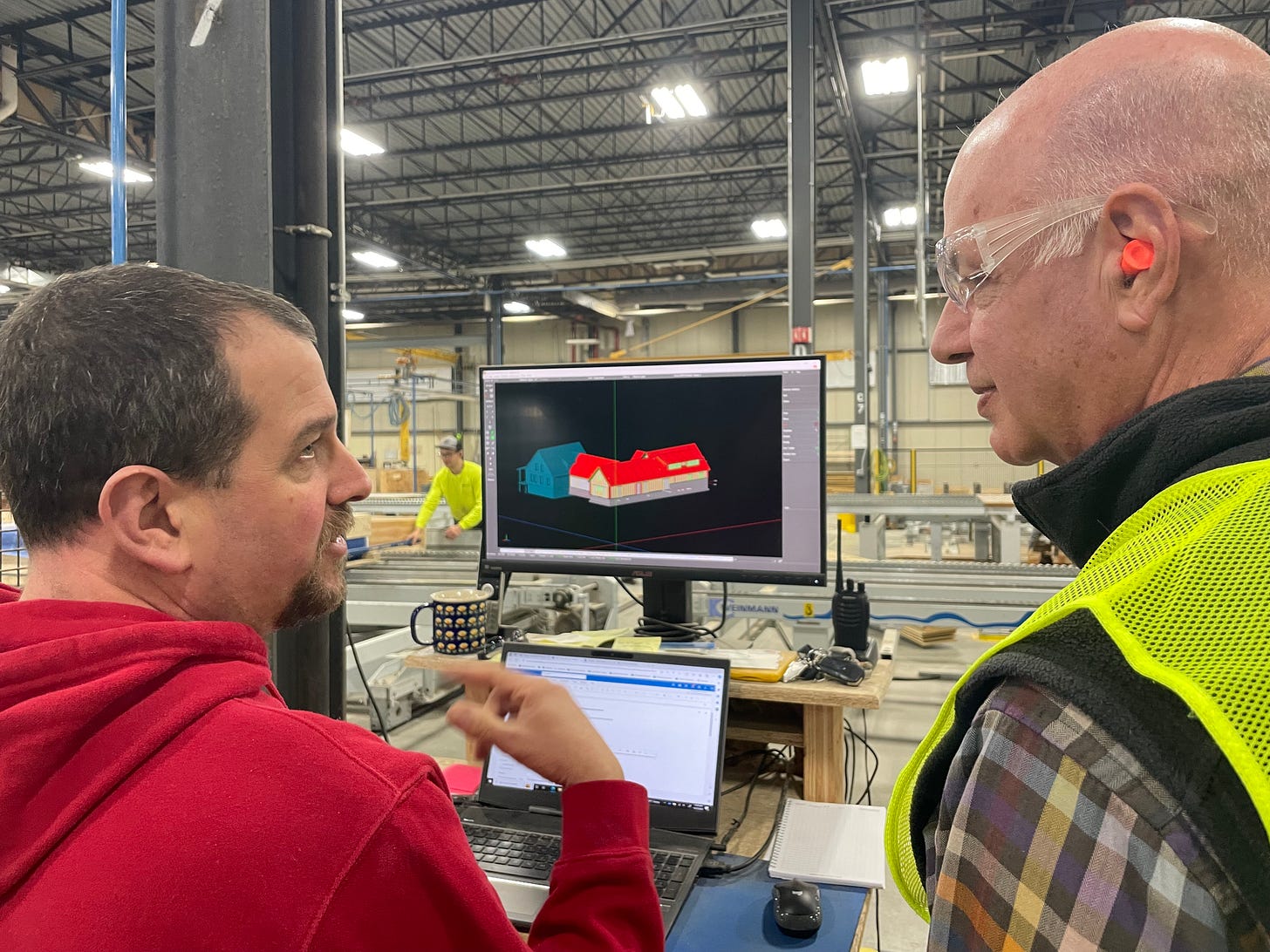
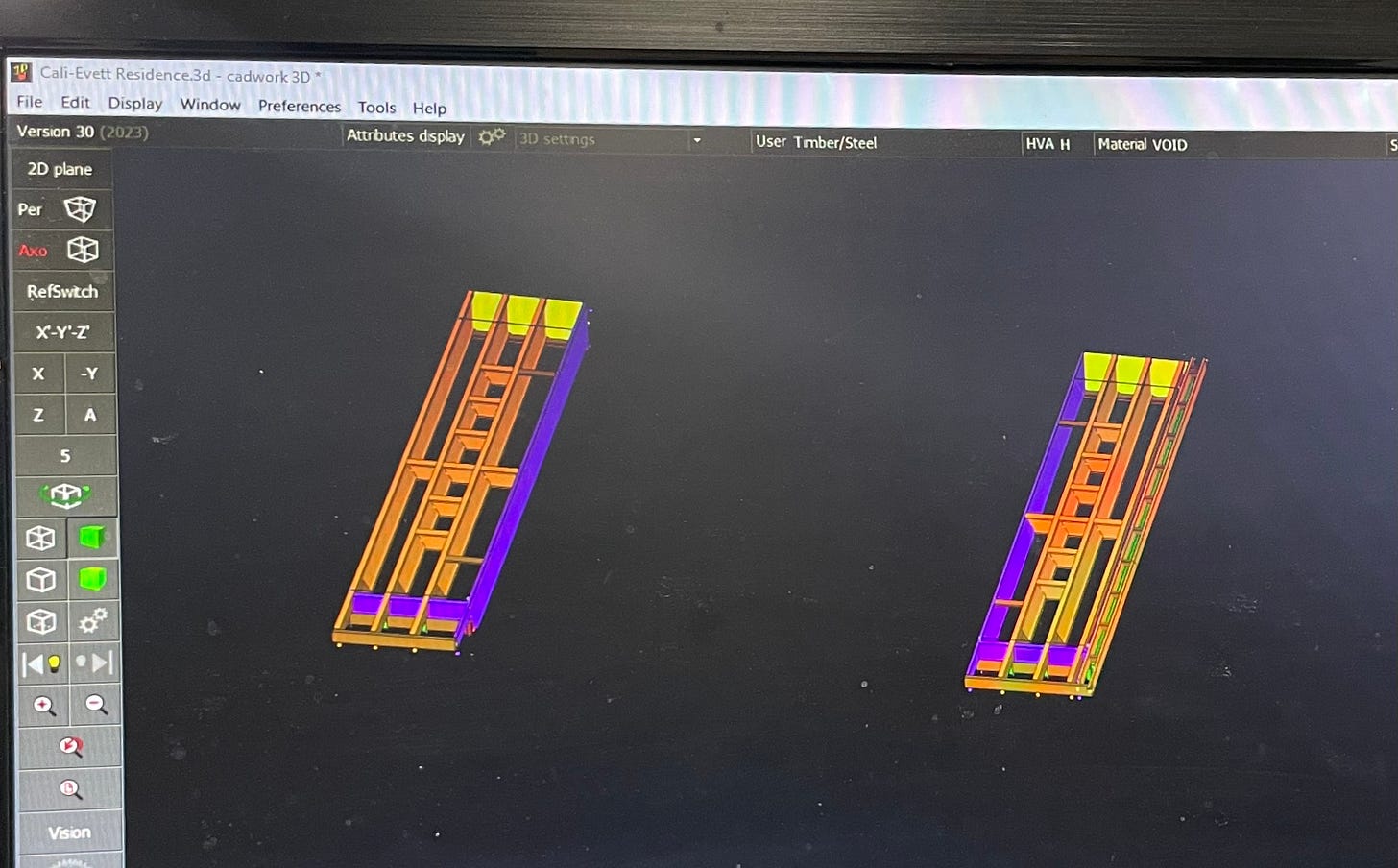
Having spent a lot of time with Dylan and Michael cutting rafter tails for the new roof over the existing house last year, I had some sense of just how exacting a process that can be at the job site. Suffice it to say, the SC-3 is WAY faster. If you want to get an idea of one in action, check out this video! It is amazing.
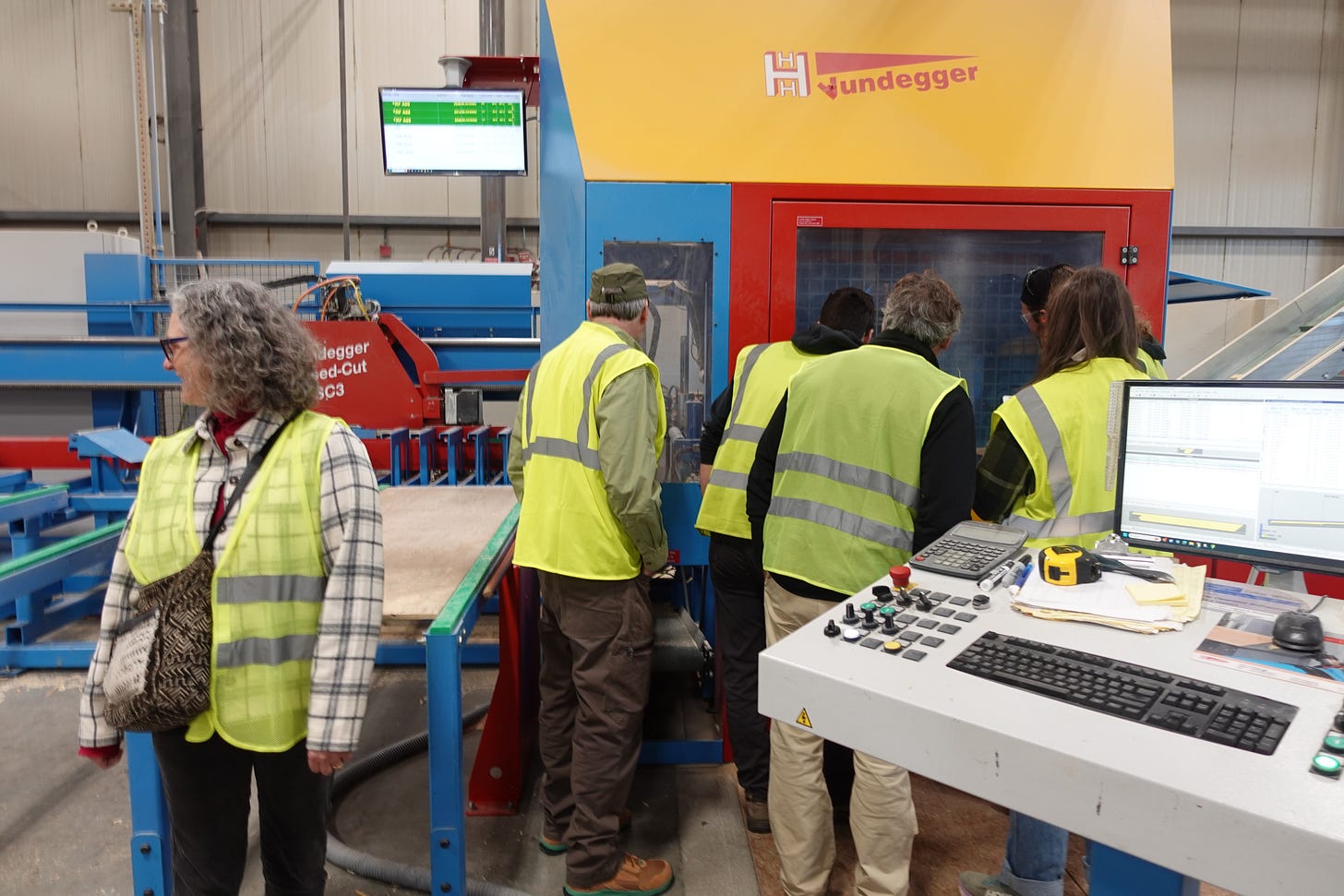
At this cutting station, engineered I-joists were fed (automatically loaded via a roller feed) into one end of the SC-3, which did all the manipulation and cutting, and sent a finished rafter out the other end. By the way, I understand the SC-3 can also drill, route, mill…a real “Edward Scissorhands” of the carpentry world! All framing elements for Bensonwood wall, floor and roof panels are cut by this machine.
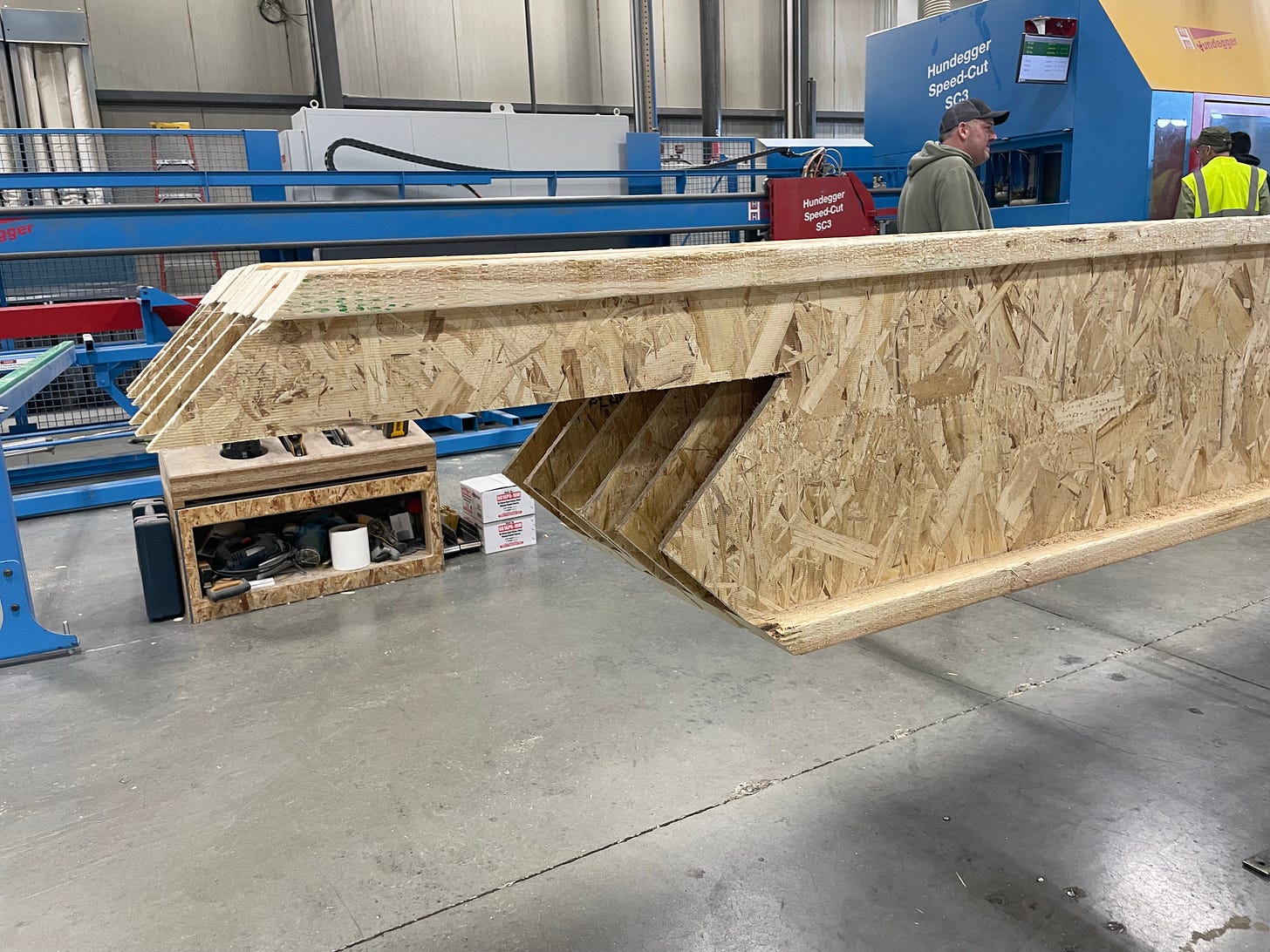
And now…the Weinmann Multifunction Bridge!
After framing elements are cut, they are brought to their respective production lines (wall, roof, floor) for framing. When we were onsite, the wall team had just finished the initial framing of a wall section, and it was moving down the line to the….Weinmann Multifunction Bridge (WMB).
Interior sheathing was set on top of the framing, and then the WMB went about its business. With the 3-D model data driving its action, the WMB nails the sheathing at specified intervals, cuts out rough openings, trims edges–all while vacuuming up its mess. It is a sight to behold. It was hard to get a great shot, but the audio alone in the video below illustrates how fast this machine is at nailing off an entire wall section. Try doing that manually on a job site in perfect conditions, let alone when it might be snowing, sleeting, or raining!
After adding framing for a service chase1 , the wall panel is flipped over (yep, via machine) so the “outside” of the wall, with empty stud cavities, is facing up and ready to go to the…
Isocell insulating machine!
The Isocell machine then fills each of the exterior stud cavities with the amount of cellulose necessary to achieve a dense pack (3.5-4 pounds per cubic foot), after which they are sent to a second WMB to add the exterior sheathing (in our case, this was Steico Wood fibre board insulation. The wood fibre insulation provides additional R-value, slows heat transfer through the studs, and leaves the assembly “vapor open” to the outside (meaning it can dry should any water make its way into the assembly).
I’ve left out some of the attentive detail the team does along the way to the above, most notably taping seams to ensure airtightness. But it was clear from what we saw, and their posted procedures, that the Bensonwood crew is careful and checks each step.
Roof panel production is a similar process as walls. The pics below show some roof insulation in process that illustrate the Isocell function.
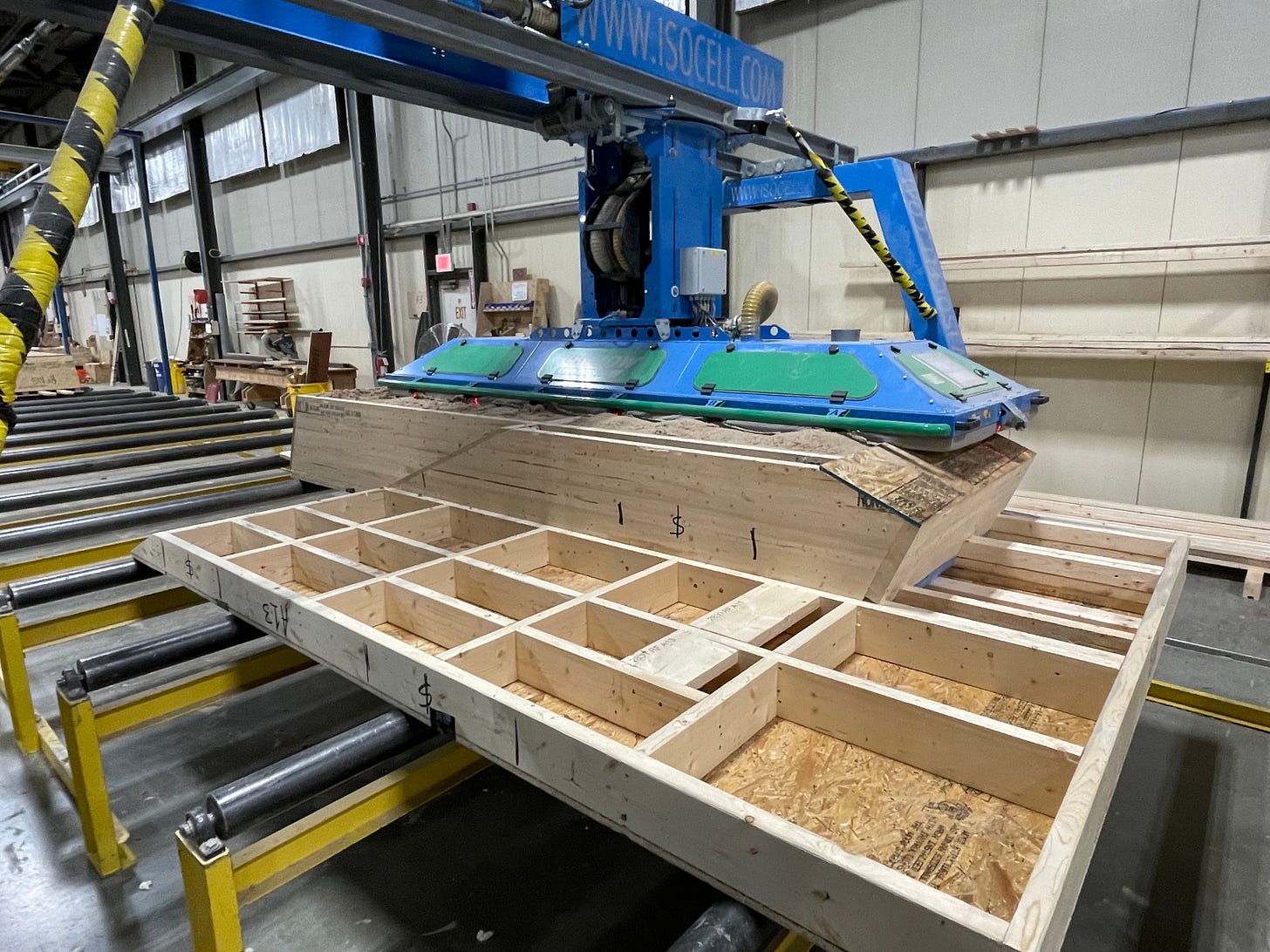
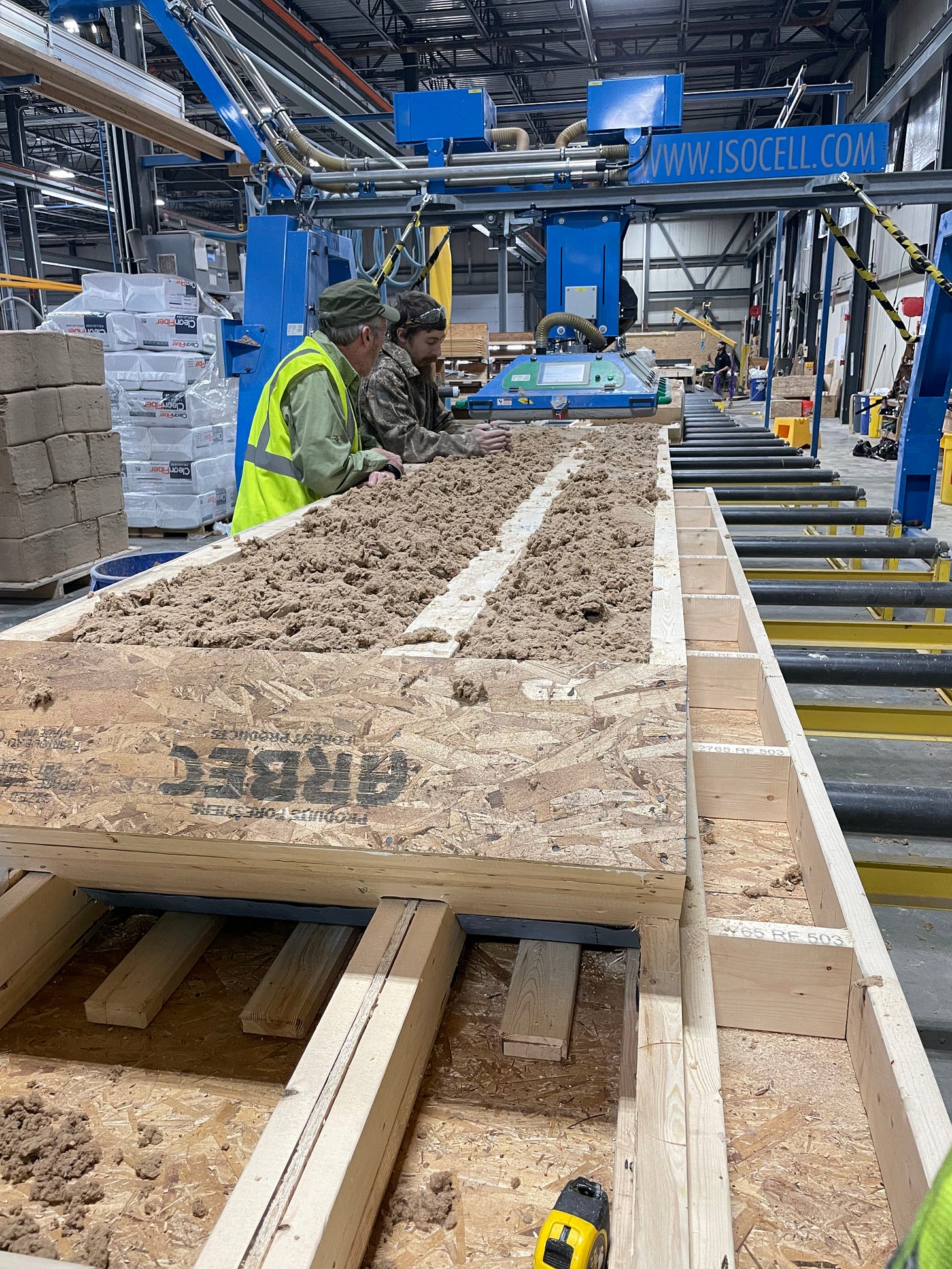
Final stop…window installation!
The other workstream we got to see was installation of windows into fully built wall sections. For the walls of our house, after insulation, they are wrapped in a weather resistant barrier membrane (blue SIGA-Majvest), and strapping is attached to allow fastening of clapboards after the building is assembled on site. When the clapboards are attached, the strapping over the sheathing creates a space between the exterior siding and the house when the that is known as a “rain screen”—if (when) any water gets past the clapboards, the gap allows bulk water to run down and out, and any wet materials to dry via the vented space. Rain screens significantly extend the longevity of the sheathing, siding, paint, and the house itself.
After all that is done, windows (and often doors, but not in our case) are installed into the rough openings.
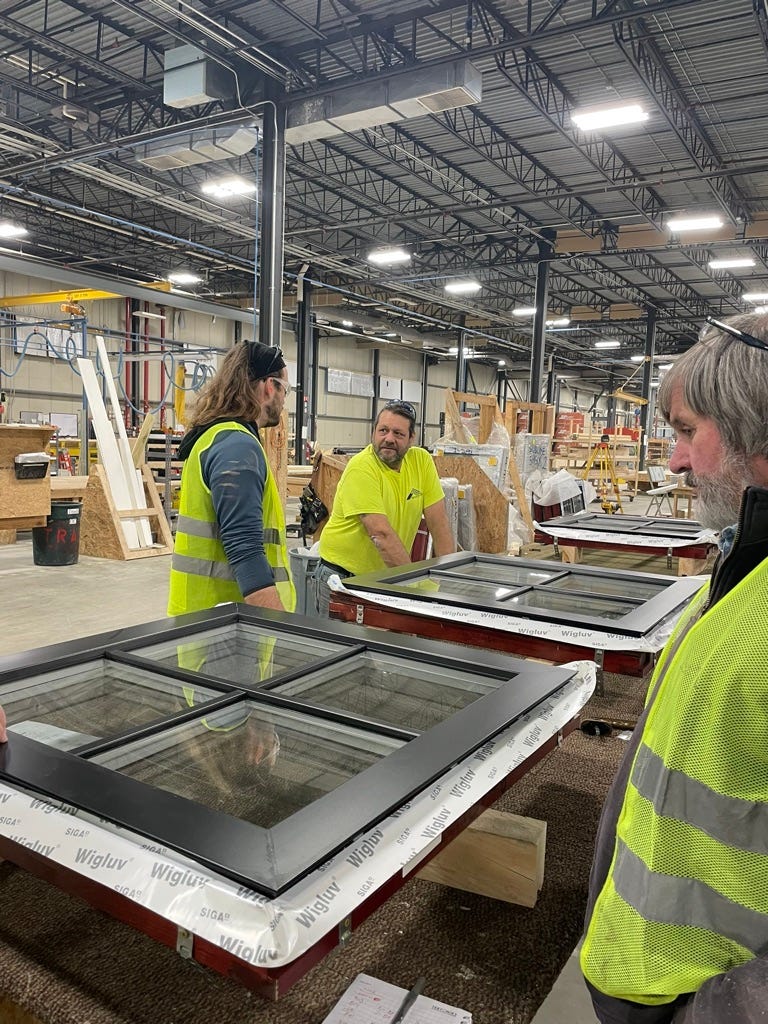
Window installation is often a problem spot in high performance homes, as details and materials are essential. Being able to install in a controlled environment, with good materials and expert installers, is a great boon. The largest windows and doors will be installed on site, and we will be paying close attention to detail to get those as nicely installed as Bensonwood was able to do here.
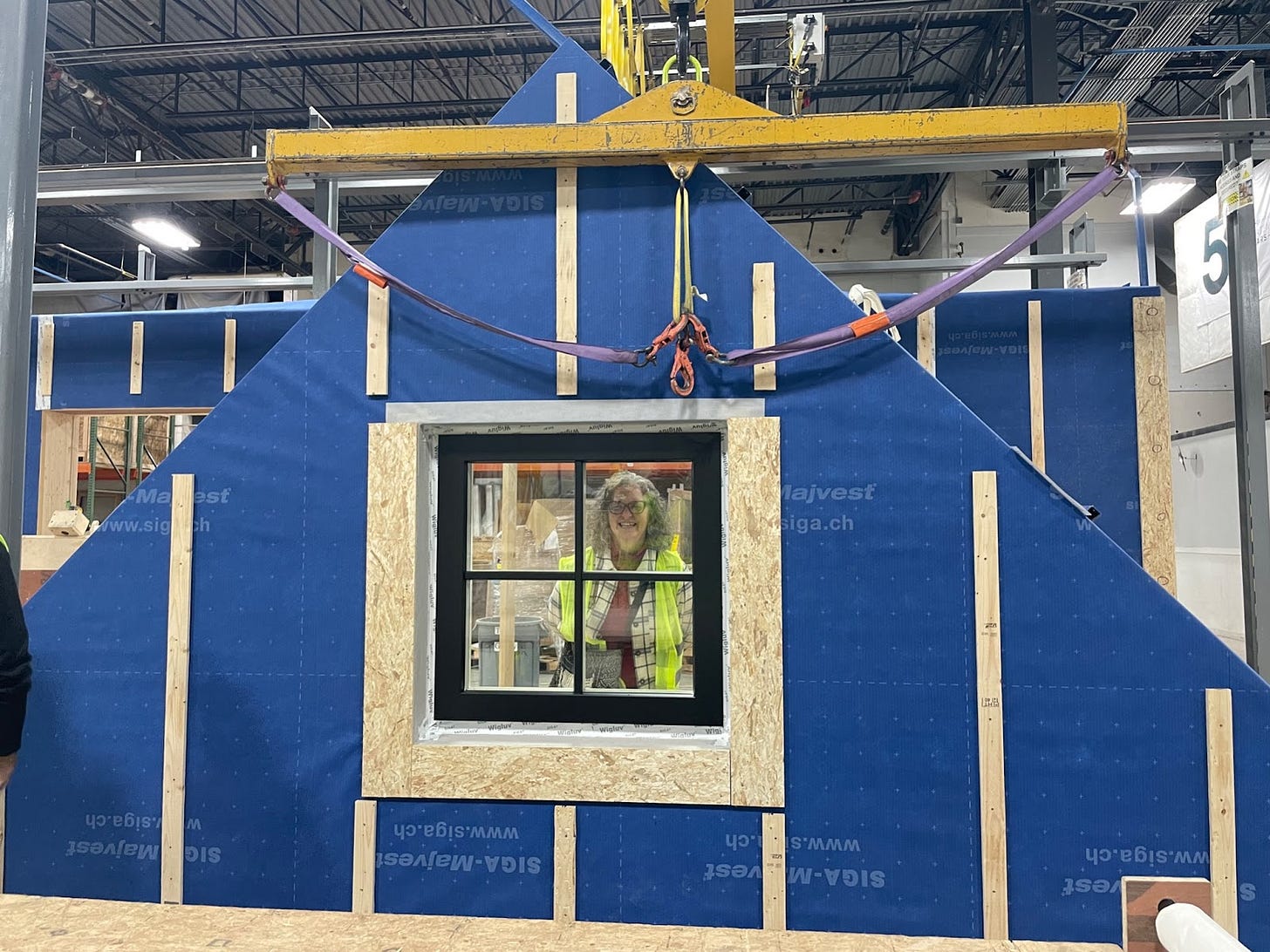
We were grateful to the Bensonwood team for hosting us that day (we also got to tour their Walpole, NH woodworking shop). We left impressed by the precision, efficiency, and care with which the Bensonwood team worked, and by the speed at which things can move using their approach to building high performance structures.
The finished panels in the parking lot made it clear that the construction was coming together…and fast! Just how fast is the topic of another post.
A little morsel:
During our visit to the woodworking shop, I spotted this little beauty of a machine! Folks who know my story will know why I enjoyed seeing the TS 750 so much. And not because it is a tilting spindle shaper…as cool as that sounds.
One of the many convenient features about the Bensonwood wall design, the service chase is vertical strapping nailed to the interior sheathing, with horizontal notches cut out so that electrical and other systems can be easily run in the wall, after which drywall is attached to the strapping.
Very cool. And love the ironwood machine :)